FDA QMSR and ISO 13485 Requirements for Practitioners and Auditors
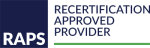
FDA QMSR Requirements Training (incl. ISO 13485) is for Practitioners and Auditors who wants to understand the requirements, including similarities, differences and key aspects of both the ISO 13485 standard and the FDA Quality Management System Regulation (Revised Part 820).
Our online training is a highly interactive way to learn at a time & pace that works best for you, making it easier to get the training you need while balancing a busy home or work life.
The Regulatory Affairs Professionals Society (RAPS) recognize this course offering global recognition for successful participants and RAPS credits for members.

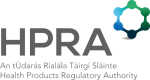

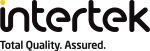
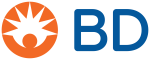
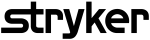
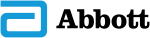
Download Brochure
View Sample Certificate of Achievement
Have 5 or more that need training?
We offer group discounts and are available for in-house (live or virtual) or tailored training in multiple formats.
Our Methodology
Not all eLearning is the same
Most other providers offer online training that is one-dimensional utilizing either Videos or PowerPoint Presentations. That is not effective training. We deploy a multi-layered methodology that offers you a New Generation of eLearning.
Course Structure Explained
eLearning Module Breakdown & Timings
An interactive, engaging eLearning experience that you can complete Anytime, Anywhere.
Time | Topic |
---|---|
60mins eLearning | Module 1 – Introduction to the new FDA QMSR
|
105mins eLearning | Module 2 – Overview of ISO 13485
Case Study! Terms and Definitions Case Study! KPIs Case Study! Risk Management and Supplier Qualification |
120mins eLearning | Module 3 – Establishing a Quality Management System
Case Study! Software Validation Case Study! Complaint Handling Records |
90mins eLearning | Module 4 – Management Responsibility
Case Study! Quality Objectives Case Study! Management Review |
75mins eLearning | Module 5 – Resource Management
Case Study! Infrastructure and Equipment Maintenance |
135mins eLearning | Module 6 – Product Realization, Part 1
Case Study! Risk Management Case Study! Customer Related Processes Case Study! Design Planning |
105mins eLearning | Module 7 – Product Realization, Part 2
Case Study! Purchasing Case Study! Calibration Requirements |
90mins eLearning | Module 8 – Measurement, Analysis, and Improvement
Case Study! Feedback Case Study! Audit Records Case Study! Audit Management Case Study! Incoming Inspection |
60mins | Certification Exam
|
Our Experts
Meet The People Behind The Course
Our experts possess a wealth of industry experience acquired over years of practical application, and in addition, they demonstrate a combination of unwavering passion and a proven aptitude for training.
Course Overview
FDA QMSR + ISO 13485 Practitioner Training
Understand how the FDA QMSR has evolved to align with ISO 13485 more closely
Outline the structure, content & requirements of both the FDA QMSR and ISO 13485
Understand the key similarities and differences between the FDA QMSR and ISO 13485
Detail the specific quality management-related requirements of the FDA QMSR and ISO 13485
Understand how auditors approach Quality Management System Audits to ensure compliance with the FDA QMSR and ISO 13485
This course would be targeted at:
- Quality Engineers
- Quality Specialists
- Internal Auditors
- Lead Auditors
- Quality Managers
- Regulatory Professionals
The Regulatory Affairs Professionals Society has approved Comply Guru (No. 1007) and recognizes this course where members will be eligible for the stated number of RAPS credits (12).
Upon successful completion, each Learner shall receive a digital Certificate of Achievement within 1 business day.
It is recommended that each Learner should have the following prior knowledge before completing this course:
- The Plan, Do, Check, Act (PDCA) cycle
- The core elements of a management system and the interrelationship between top management responsibility, policy, objectives, planning, implementation, measurement, review, and continual improvement.
- The fundamental concepts and commonly used quality management terms and definitions
In order to successfully complete this course, each Learner will need to:
- Complete the eLearning modules & associated end-of-module assessments
- Obtain 70% or higher in the final end-of-course assessment (MCQ-based)
There are recommended requirements for each Learner in wishing to complete any of our eLearning modules. In our experience, Workplace IT environments’ internal configurations and available software can vary (new or old), and there may be various limitations or other restrictions in place, and as such, the functionality of any Learning Management System (LMS) may be impacted, restricted and may not perform well. Read the full technology requirements here.
Watch and Learn More
About Our Requirements Training
Learn about how our eLearning methodology is leading the industry for innovation through online learning
Customer Reviews
What Our Learners Are Saying
Read verified reviews from Learners who have completed this course.
4.3
Average Rating
22 global ratings
-
Excellent virtual training format
-
Professional and fun course
-
The course was comprehensive but a little bit long.
-
It was a very good and understood training
-
Training was informative and easy to understand. Case studies were very helpful.
Frequently Asked Questions